Software
Thanks to TecSA Software Package, the Customer is completely autonomous in defining, managing and elaborating the tests.
TecSA Software can be installed in whatever operating system. Data entered by the user and the test results can be exported in .CSV format and imported in Excel or Diadem.
The computer system architecture to control the dynamometer bench is composed by three levels.
First Level (optional): centralized management of the data archives and results analysis
Second Level: supervision of the dynos, monitoring and results analysis. It is possible to use one or more PCs connected to a LAN that can be installed in different offices
Third Level: control of the dynamometers, composed by a PC connected to a PLC and to a system based on DSP micro controller, that manages the activity in Real Time
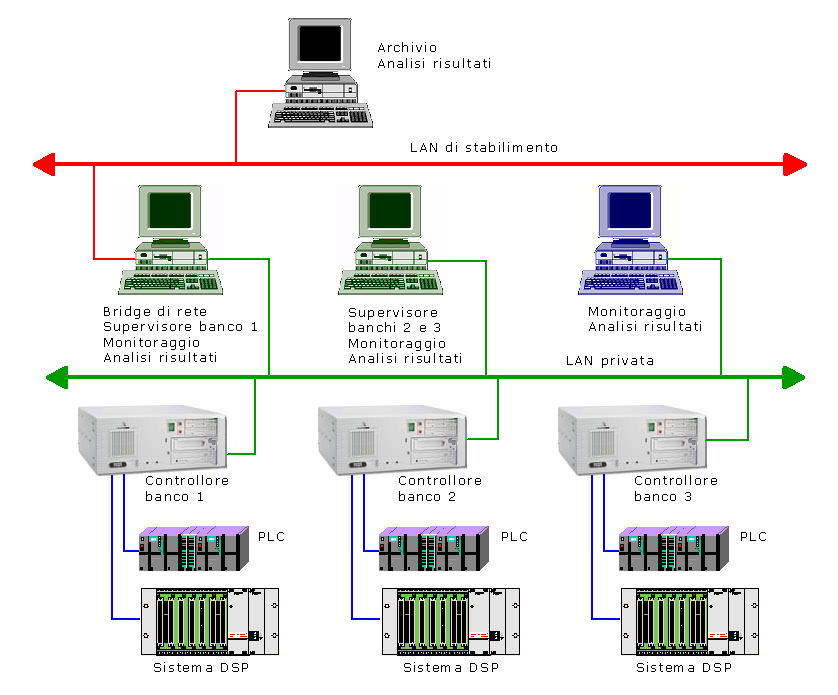
Real Time system
Real Time system is composed of NI cRio with CPU and an expansion chassis and it is managed at 1 kHz frequency. Thanks to Real Time system it is possible to carry on brake applications:
- in torque
- in pressure
- in deceleration
- in torque, by setting up the max. applicable value of pressure
- in torque, pressure and deceleration, with possibility to modify the control value during the braking
- in torque, pressure and deceleration, with possibility to apply trigonometrical functions
- with fixed or variable inertia according to the deceleration to simulate the transfer of the load on the vehicle (from back to front)
- with external hand brake
- static friction, hill hold, creep groan and sticking
TecSA Software and TECNAS System
In particular, TecSA Software allows to perform:
- profiles simulation on road/WLTP: the dyno performs the brake applications of the vehicle on a circuit (typically used for the racing sector)
- regenerative braking/blending: the dyno replies the braking conditions of the electrical and hybrid vehicles, by adding the application of both the pneumatic and the electric brakes
TECNAS (TecSA Noise Acquisition System) provides each TecSA machines with two different capabilities:
- performance Tests
- NVH (Noise Vibration Harshness) Tests, to analyse the comfort of a vehicle
TECNAS Hardware and Software
TECNAS hardware is composed by:
- 8 vibro-acoustic channels (24 bit, 110 dB dynamic field, 102.4 kS/s max. 45 kHz alias-free bandwidth, IEPE/ICP conditioning)
- 4 auxiliary channels at 100 Hz (pressure, torque, temperature, speed)
TECNAS software allows:
- three different buffers for FFT (1024, 20148, 4096)
- online calculation of FFT, noise/vibration, peak/frequency
- programmable threshold
- automatic generation of report
- audio file acquisition
- sound output for megaphone
- cascade post-elaboration
The description of new test procedures is particularly easy. TecSA programs allow the user to individually define each braking by adding more than 200 parameters, to gather the brake applications in phases and cycles and to set-up the repetitions.
The performance of new tests is completely automated and the constant presence of an operator is not needed. A single workstation allows the monitoring (including remote control, via tablet and smartphone) of the activities of several machines and the transfer of the results to centralized databases.
At the end of the test the computerized system elaborates numerical results (values are subdivided for each brake application) and Time History data (acquired values according to the specifications defined by the user). Time History file is generated in standard format .CSV that can be read on whatever electronical device.